RVA SERVICES
Asset operational lifespan
There was a time when decommissioning specialists would be brought into a project when an asset was already redundant. However, enlisting the support of engineers with a decommissioning mindset throughout the entire operational lifespan of an asset, is increasingly being acknowledged as a value-adding exercise. That’s because, if the operator has taken a proactive approach to ongoing maintenance and provisioning, they will be empowered with a far greater degree of data and knowledge when the time comes to embark on the decommissioning exercise itself.
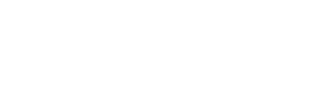
Professional engineers and technical advisers
Many clients engage us years – if not decades – before a decommissioning project is due to begin, choosing to enlist our engineering support to devise robust asset baseline decommissioning and longer-term liability plans. Such dynamic instruments empower operators to make informed decisions about the scheduling, budgeting and preparation for works at every stage in an asset’s lifecycle, while helping to minimise risk of unknowns and controlling costs.
Our technical advice can be called on for ad-hoc decommissioning guidance and expertise, or more comprehensive preparatory schemes.
Environmental permit surrender and lease exit support
It is often the case that assets are gradually taken offline but the dismantling and clearance process is delayed. In such circumstances, we develop robust procedures and systems to protect the integrity of these structures and make them safe. This role also sees us routinely advise on matters such as decommissioning strategies, fit-for-purpose decontamination regimes with appropriate documentation provision ahead of a lease exit, and liaison with enforcing authorities regarding regulatory declassification and environmental permit surrender.
Financial provisioning
Our operational asset management and retirement provisioning insight regularly acts as the foundation for robust financial management tools which enable plant owners to confidently accrue adequate funds for an asset’s eventual ‘end of life’ decommissioning.
This commercial resource can further be used to help conduct periodic assessments of plant viability against future liabilities, the evaluation of costs for retrofitting plant, and raise realistic cost awareness for the acquisition and divestment of assets, to name just a few.
Our engineers have also developed an auditable, robust and flexible asset retirement support service specifically designed to enable accounting standards compliance on large scale and high value production assets. The associated standards vary from site to site, but examples include FAS143 and IAS 37.
Decommissioning, demolition and site clearance options and feasibility studies
This detailed type of costing exercise considers a number of variables – including short and long-term safety, environmental, security, commercial and financial factors relevant to the site and/or asset(s) concerned – and sees RVA produce a comprehensive document which explores a number of possible project approaches.
More detailed than a costings estimate, the resulting report may include divestment options, the development of expressions of interest, potential demolition phasing and methodologies, hazardous materials detail, remediation requirements, EHS priorities, the surrender of permits and licenses, and more. By disclosing all known opportunities and threats, complete with recommendations, clients are presented with a clear and focused management tool from which informed and robust business decisions can be made.
SSE Generation required a high level but robust assessment of its liabilities to assist in the determination of adequate provision for business and reporting purposes.
RVA were able to demonstrate both the experience and industry data to make such an assessment at an appropriate level of detail and respond in a relatively short time from instruction to proceed.
Plant upgrade and modifications
There can be a tendency to presume that decommissioning works represent the rationalisation of an organisation’s operations or the complete closure of a site. However, there are of course instances whereby an upgrade or overhaul of assets is required to reflect a manufacturer’s expansion or advancement.
For such projects, RVA can assist with planning for the surgical, ultra-precise and often sequential dismantling and extraction of specific assets, to facilitate a plant retrofit. With such works commonly carried out on live sites, in parallel with new assets being installed to minimise processing downtime, these are major logistical exercises as well as highly complex technical undertakings.
Asset recovery for sale or relocation
With many manufacturing sectors undergoing major ongoing change, it is not uncommon for multinational organisations to approach RVA to help relocate assets to overseas production sites or explore their sale to third parties. The latter option is particularly attractive when rationalising or closing plants, as it helps to minimise the costs of wider decommissioning works. However, there are no hard and fast rules as to which assets can and cannot be recovered.
There are several different approaches that can be taken. From the recovery of individual items of plant, to the dismantling of entire processes for shipment and reinstallation elsewhere, if viable, RVA will devise the optimum outcome for every situation. Our objective is to provide realistic assessments and manage expectations, so that the most beneficial strategies may be selected and asset monetisation maximised. Factors such as the complexity and age of plant, its former process, the cost of recovery, transport, re-installation, testing, market forces and economics, commercial confidentiality and competition will all form part of the decision-making procedure.
Decommissioning strategy and planning
Decommissioning is often considered as an extension of site maintenance. But preparing assets for a restart is very different to permanently isolating services and decommissioning the asset entirely because it has reached its end of life.
This is not to say actions would purposefully be missed by an operator’s internal personnel – most will no doubt approach their role with maximum care and attention. But rarely do such individuals have a decommissioning mindset. In fact, they could go to opposite extremes and undertake some tasks they don’t actually need to, as they could be handled more efficiently – and ultimately, safely – at the dismantling phase.
Drawing upon decades of planning, decontamination, dismantling, demolition and sector-specific knowledge, RVA is therefore well equipped to devise and audit bespoke decommissioning strategies, which strategically explore all options that the client may not have otherwise considered.
When should a decommissioning engineer get involved?
Some regulatory frameworks stipulate that a principal designer should be appointed on decommissioning projects to ensure works are rigorously planned from start to finish, and the right people do the right job at the right time, armed with the information they need to effectively manage and mitigate risks. This is why decommissioning specialists are increasingly being consulted even during the earliest phases of an asset’s
Physical, virtual or hybrid decommissioning support
When it comes to our provision of decommissioning services, we can adopt varied deployment methods, including a physical on-site presence, virtual support, or a hybrid approach. Exactly what is feasible will depend on the scope of work involved, and decisions will always be made on the grounds of safety. However, where possible we will actively seek to make best use of technology and remote or geographically diverse resources, to reduce the unnecessary carbon impact of travel, and keep programmes progressing fluidly whatever else may be going on in the world.